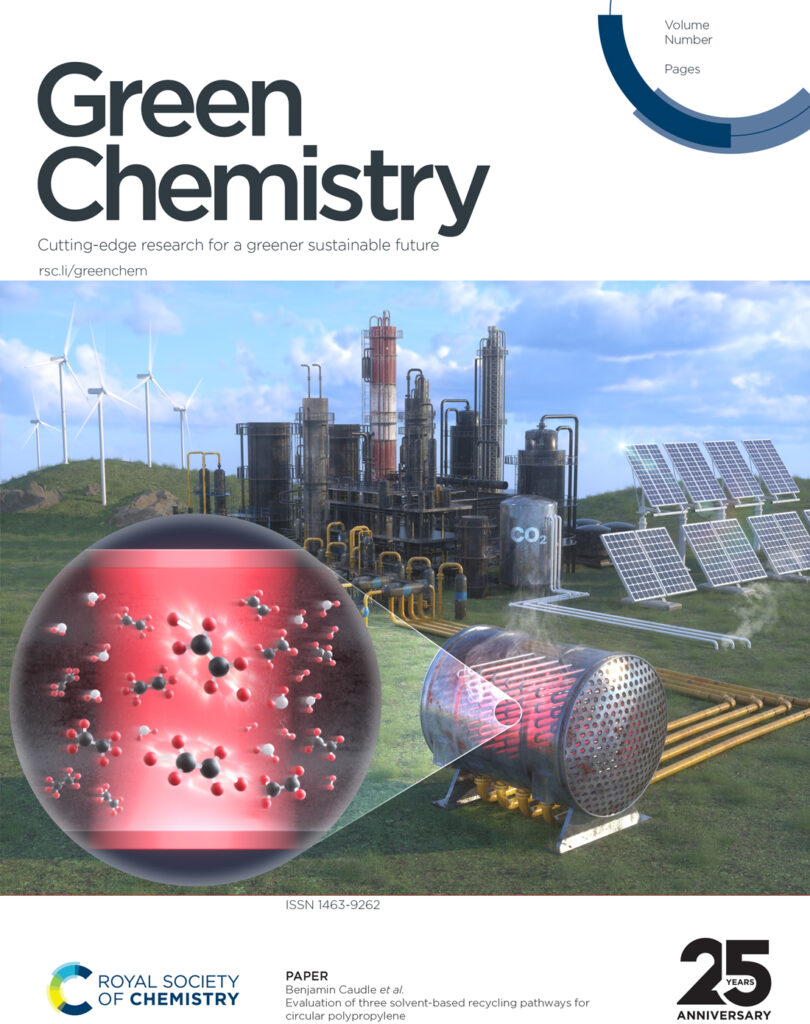
https://pubs.rsc.org/en/journals/journalissues/gc#!issueid=gc027014&type=current&issnprint=1463-9262
Journal cover / Green Chemistry 14 April 2025, Issue 14,
Abstract
Ethylene, a building block of the chemical industry, significantly contributes to global greenhouse gas (GHG) emissions, prompting interest in decarbonization approaches to align with recent carbon neutrality initiatives. This paper presents a comprehensive techno-economic analysis (TEA) and life cycle analysis (LCA) of GHG emissions, comparing conventional ethane-based ethylene plants with three decarbonization approaches. The study was conducted within the context of the U.S. average, with sensitivity analysis to identify key drivers affecting well-to-gate (WTG) GHG emissions and the levelized cost of ethylene (LCOE). The conventional plant exhibited a GHG emission of 869 kgCO2e per tonne-ethylene and a LCOE of $746 per tonne-ethylene. Substituting external natural gas fuels with grid or renewable electricity decreased the emissions to 806 and 717 kgCO2e per tonne-ethylene, respectively. The emissions of the grid-powered or renewable-powered electrically heated cracker that exports co-produced hydrogen to substitute conventional gray hydrogen were 1031 and −163 kgCO2e per tonne-ethylene, respectively. The application of CCS to purge gas showed 703 and 514 kgCO2e per tonne-ethylene emissions, respectively. The electric cracker showed lower emissions than the conventional plant below 380 kgCO2e per MW h electricity upstream, and at 60 kgCO2e per MW h, it achieved carbon neutrality. Regarding LCOE, when using a grid electricity source, no external natural gas, electric cracker, and adding CCS to purge gas showed $743, 833, and 771 per tonne-ethylene, respectively. When these plants adopt renewable electricity, their LCOEs will be $737, 746 and 757 per tonne-ethylene. Below $41.1 per MW h electricity price, the electric cracker had the lowest value among all cases. With hydrogen prices of $0.5–3.0 per kg-H2, the electric cracker’s LCOE ranged from −$45(cost)–128(saving) per tonne-ethylene compared to the conventional concept.